By Katrina Gonzalez ’17
Discoveries on the microscale have opened new realms of scientific study.
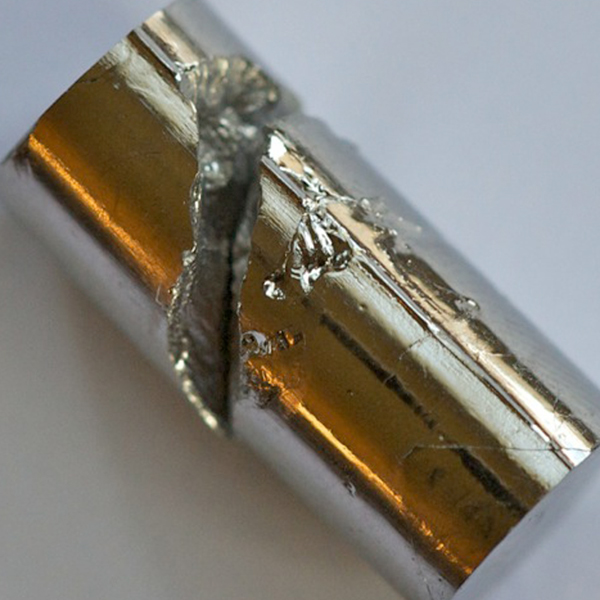
When we think of technology, it’s often robots or planes that come to mind. It’s easy to marvel at the idea of a metal skeleton taking flight or a delicately built android weaving its way through a crowd. Looming skyscrapers and bridges spanning horizons are not only
However, there are a host of innovations and inventions being made on the nanoscale. Specifically, there are entire fields devoted to the optimization of structures and atomic interactions. In particular, materials science and nanotechnology have piqued interest with the advent of computers. Before the creation of computers and the general push to make devices smaller, it was acceptable to just expand. Materials didn’t need to be bettered because their resulting structures could simply be reinforced or braced without regard to size. The 1920’s – the decade that directly preceded the invention of the computer – was defined by its tendency towards excess, towards towering skyscrapers and hulking automobiles. However, the push towards compactness that took place with the creation of the integrated circuit has essentially given materials science a new place of prominence, thereby allowing the field of nanotechnology.
In particular, recent advancements in materials science, with the creation of bulk metallic glasses, have led to the creation of smaller, more durable materials suitable for motor gearing and micro-mechanical electrical systems. Metallic glasses (MG) are created by cooling metallic alloys such that they solidify immediately, without time for their molecules to form a crystalline pattern. This limits any kind of large scale periodicity, and translates into large clusters of molecules packed tightly together. This packing density imbues the material with a multitude of unique characteristics: most notably its hardness and ability to resist wear. This is due to the high Young’s modulus of elasticity of the material, meaning that it exhibits relatively little plastic, or non-reversible, deformation even under high amounts of stress. For parts such as gears, this quality allows for a longer, higher quality lifespan. Additionally, casting of metallic glasses results in a more detailed, precise solid because of the lack of periodicity. For crystalline structures to break cleanly, they must reach some terminal point within their structure. However, MGs lack that inherent order and can therefore fill a given mold well and flush with all of the indentations. On top of that, MGs shrink less upon cooling than their respective metallic alloys, meaning that they adhere better to any molds, regardless of size. For these reasons, MGs are one of the foremost materials that can be used to create ever-shrinking components and devices.
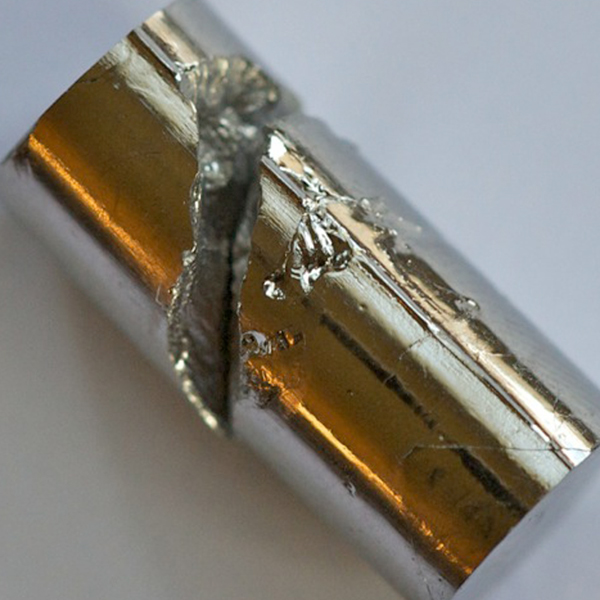
In the same way that MGs exploit the characteristics that come with an amorphous solid, nanotechnology is based off of the properties that nanoparticles and other very small structures exhibit. For particles under 100 nanometers, surface area dominates in comparison to volume. Though this can occur on a macroscale level, the degree to which it happens on the nanoscale is unsurpassable. In particular, nanomaterials often have very unique optical and structural properties, as well as greater diffusivity, a measure of the rate at which particles or heat or fluids can spread. However, though nanoparticles have become more ubiquitous over the past few years due to their use in synthetic vaccines and cancer treatment, both MGs and nanoparticles are still not widespread within the manufacturing industry. For MGs, it is because they are hard to fabricate on a larger scale. For nanoparticles, it is because most methods of synthesis are either inherently wasteful or hard to control. So for now, skyscrapers and robots reign as the face of modern-day engineering. They continue to populate science fiction and news, but new fields are emerging. And despite their size, or lack thereof, they may just be able to eclipse those looming feats.